Air Compressor Technology: Latest Innovations and Benefits
The evolution of compressor technology
Air compressors remain essential equipment across numerous industries, from manufacturing and construction to automotive and healthcare. Recent technological advancements have transformed these erstwhile simple machines into sophisticated systems that deliver improved efficiency, reliability, and performance. These innovations address longstanding challenges while open new possibilities for compressed air applications.
Understand these technological developments is crucial for businesses look to optimize their operations, reduce costs, and minimize environmental impact. Let’s explore the virtually significant innovations reshape the compressor landscape.
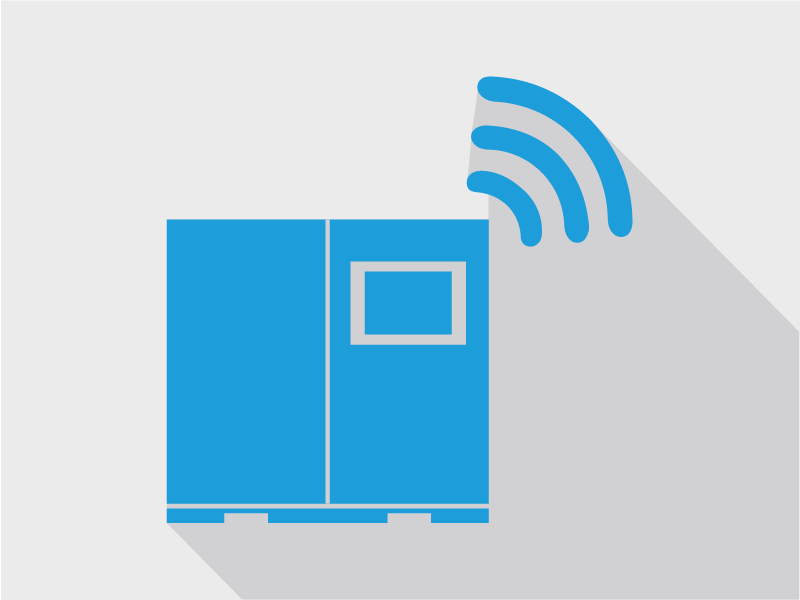
Source: mark compressors.com
Variable speed drive technology
Peradventure the virtually transformative development in modern compressors is the widespread adoption of variable speed drive (vVSD)technology. Unlike traditional fix speed compressors that operate at full capacity irrespective of demand, vsVSDompressors adjust their motor speed to match the rerequirementir output.
How VSD technology work
VSD compressors utilize frequency inverters to regulate the electrical supply to the motor, allow precise control over rotation speed. This dynamic adjustment capability mean the compressor produce solely the amount of compress air need at any give moment.
Benefits of VSD technology
- Energy efficiency: VSD compressors typically reduce energy consumption by 20 50 % compare to fix speed models. Since compressors account for a significant portion of industrial electricity usage, these savings can considerably impact operational costs.
- Reduced wear and tear: By eliminate the frequent start stop cycles common in conventional compressors, VSD technology minimize mechanical stress, extend component lifespan.
- Consistent pressure: VSD compressors maintain stable pressure levels, improve the performance of pneumatic tools and equipment.
- Soft starting: The gradual ramp up of motor speed eliminate high inrush currents, reduce electrical stress on both the compressor and facility power systems.
When implement right, VSD technology offer one of the fastest returns on investment among compressor upgrades, oftentimes pay for itself within 1 2 years through energy savings exclusively.

Source: micoope.com.GT
Oil free compressor advancements
While oil lubricate compressors remain common, oil free technology has make significant strides in performance and reliability. These advancements are specially valuable for applications require contaminant free air, such as food processing, pharmaceuticals, electronics manufacturing, and healthcare.
Next generation oil free designs
Modern oil free compressors utilize advanced materials and precision engineering to achieve reliable operation without lubrication. Innovations include:
- Water injected screw technology: Use water alternatively of oil for cool and sealing, these compressors deliver 100 % oil free air while maintain excellent efficiency.
- Ceramic and polymer components: Heat-resistant, self lubricate materials reduce friction and wear without require oil.
- Two stage compression: By divide compression across multiple stages with intercooler, these systems achieve higher efficiency while maintain oil free operation.
Benefits of advanced oil free technology
- Elimination of contamination risk: Critical for sensitive applications where yet trace oil can compromise product quality or safety.
- Reduced maintenance: No need for oil changes, filter replacements, or oil separation systems.
- Lower environmental impact: No oil disposal concerns or risk of leakage.
- Improved air quality: Deliver ISO 8573 1 class 0 air purity, the highest possible standard.
The gap in efficiency between oil free and oil lubricate compressors has narrow importantly, make oil free options progressively viable for a broader range of applications.
Smart monitoring and IOT integration
The integration of internet of things (iIOT)technology has rerevolutionizedompressor monitoring and management. Modern compressors nowadays incorporate sophisticated sensors, connectivity features, and analytics capabilities that transform maintenance and operation.
Key smart monitoring features
- Real time performance tracking: Continuous monitoring of critical parameters include pressure, temperature, power consumption, and runtime.
- Predictive maintenance: Advanced algorithms analyze operational data to predict potential failures before they occur, allow for scheduled maintenance preferably than emergency repairs.
- Remote monitoring and control: Cloud base platforms enable operators to monitor and adjust compressor settings from anyplace via smartphone, tablet, or computer.
- Automated alerts: Instant notifications when parameters deviate from optimal ranges, allow quick intervention.
- Performance analytics: Detailed reports on efficiency, energy usage, and operational patterns help identify optimization opportunities.
Benefits of smart monitoring
- Reduced downtime: Predictive maintenance can decrease unplanned downtime by up to 70 %.
- Extended equipment life: Address minor issues before they escalate help preserve compressor components.
- Optimized performance: Data drive adjustments ensure the compressor operate at peak efficiency.
- Lower maintenance costs: Condition base maintenance replaces schedule service intervals, reduce unnecessary parts replacement and labor.
Many manufacturers nowadays offer comprehensive monitoring packages that integrate with exist building management systems, provide centralized control of the entire compress air system.
Energy recovery systems
A fundamental law of physics dictates that compress air generate heat — in fact, some 90 % of the electrical energy use by an air compressor converts to heat. Instead, than allow this thermal energy to dissipate as waste, modern compressors progressively incorporate energy recovery systems.
Types of energy recovery solutions
- Air to water heat exchangers: Transfer heat from the compressor to a water circuit for facility heating, process water, or domestic hot water.
- Air-to-air recovery: Captures hot air from the compressor for space heating or process applications.
- Integrated heat recovery modules: Factory install systems design specifically for efficient heat capture and transfer.
Benefits of energy recovery
- Dramatic cost savings: Up to 94 % of input electrical energy can be recovered as useful heat, importantly reduce heating costs.
- Reduced carbon footprint: Lower fuel consumption for heating translate to reduce emissions.
- Year round utility: Flush in warm seasons, recover heat can be used for process water or redirect outside.
- Quick ROI: Energy recovery systems typically pay for themselves within 1 3 years, depend on usage patterns and energy costs.
For facilities with substantial heating needs, energy recovery represent one of the virtually financially attractive compressor upgrades available.
Advanced control systems
Modern compressor control systems have evolved far beyond simple pressure switches. Today’s controllers utilize sophisticated algorithms and connectivity to optimize performance across multiple compressors and auxiliary equipment.
Key control technologies
- Master controllers: Coordinate multiple compressors to operate as a unified system, select the virtually efficient combination to meet demand.
- Adaptive control: Learn usage patterns over time and anticipate demand changes, adjust operation proactively preferably than reactively.
- Pressure band optimization: Maintain pressure within narrower bands, prevent energy waste from excessive pressure.
- Sequential control: Intelligently manage multiple compressors of different types and sizes to maximize system efficiency.
- Integrated auxiliary management: Control dryers, filters, and condensate management systems in harmony with compressors.
Benefits of advanced control
- System-wide efficiency: Optimize the entire compress air system instead than individual components can yield 10 15 % additional energy savings.
- Balanced component usage: Yet distribution of runtime across multiple compressors extend equipment life.
- Pressure stability: Tighter pressure control improve the performance of pneumatic equipment while reduce air consumption.
- Simplify management: Centralized control reduce operator intervention and ensure consistent operation.
These control systems oftentimes feature intuitive touchscreen interfaces and visualization tools that make complex system management accessible eventide to non-specialist operators.
Noise reduction technology
Historically, compressors were notorious for their noise levels, oftentimes require isolation in separate rooms. Recent innovations have dramatically reduce operational noise, allow compressors to be install airless to point of use without create disruptive work environments.
Modern noise reduction approaches
- Advanced enclosure design: Multi layer sound insulation with specialized materials absorbs and block noise transmission.
- Vibration isolation: Sophisticated mount systems prevent vibration transfer to surround structures.
- Optimized airflow paths: Redesign intake and cool systems reduce turbulence relate noise.
- Low speed operation: Especially in VSD compressors, slower operating speeds produce less noise during partial load operation.
- Resonance mapping: Computer modeling identifies and eliminates resonant frequencies that amplify noise.
Benefits of quieter compressors
- Improved work environment: Reduced noise exposure enhance worker comfort and communication.
- Flexible installation: Quieter compressors can be installed in or near production areas, save on pipe costs and pressure drop.
- Regulatory compliance: Easier adherence to workplace noise regulations without additional sound attenuation measures.
- Lower infrastructure costs: May eliminate the need for dedicated compressor rooms with specialized soundproofing.
Many modern compressors nowadays operate at noise levels below 70 DBA — comparable to normal conversation — represent a dramatic improvement over previous generations that routinely exceed 85 DBA.
Compact and modular designs
Space constraints represent a significant challenge for many facilities. Modern compressor designs address this through innovative packaging that reduce footprint while improve accessibility for maintenance.
Space-saving innovations
- Vertical integration: Stack components vertically quite than horizontally reduce floor space requirements.
- Entirely in one system: Compressors with integrated dryers, filters, and receivers eliminate the need for separate components.
- Modular construction: Standardized modules that can be configured to meet specific requirements while optimize space usage.
- Service oriented design: Strategic component placement ensure maintenance can be performed with minimal clearance requirements.
Benefits of space efficient designs
- Reduced footprint: Modern integrated systems can require up to 30 % less floor space than equivalent separate components.
- Simplified installation: Pre engineer packages reduce installation time and complexity.
- Future flexibility: Modular systems can be reconfigured or expand as needs change.
- Improved maintenance access: Despite smaller footprints, thoughtful design oftentimes improve service accessibility.
These compact designs are peculiarly valuable for facilities with limited space or those look to repurpose exist compressor rooms for production activities.
Environmental and sustainability improvements
As environmental considerations become progressively important, compressor manufacturers have respond with designs that reduce ecological impact throughout the product lifecycle.
Key environmental innovations
- Low GWP refrigerants: Refrigerated dryers nowadays use refrigerants with lower global warming potential.
- Water conservation: Closed loop cool systems dramatically reduce water consumption in water cool compressors.
- Eco-friendly materials: Increase use of recyclable components and reduction of hazardous materials.
- Zero waste condensate management: Advanced oil water separators that produce discharge water clean adequate for direct drainage.
- Extended service intervals: Retentive last consumables reduce waste and maintenance requirements.
Sustainability benefits
- Reduced carbon footprint: Energy efficient operation and eco-friendly materials minimize environmental impact.
- Lower resource consumption: Decrease requirements for water, oil, and replacement parts conserve natural resources.
- Regulatory compliance: Frontwards look designs meet or exceed emerge environmental regulations.
- Corporate sustainability goals: Help organizations achieve document environmental improvements.
Many manufacturers nowadays provide environmental impact statements and lifecycle analyses to help customers understand and quantify the ecological benefits of their compressor choices.
Conclusion: the future of compressor technology
The pace of innovation in compressor technology show no signs of slow. Current development trends point toward eventide more efficient, intelligent, and customizable systems in the come years. Businesses invest in modern compressor technology not sole realize immediate benefits in efficiency and reliability but likewise position themselves to adapt to future energy and operational challenges.
When evaluate new compressor technology, organizations should consider their specific application requirements, growth projections, and total cost of ownership sooner than focus exclusively on initial purchase price. The virtually significant long term value oftentimes come from technologies that optimize energy consumption, reduce maintenance requirements, and provide operational flexibility.
By embrace these technological advancements, businesses can transform what was erstwhile view as simply a utility expense into a strategic asset that enhance productivity, sustainability, and profitability.